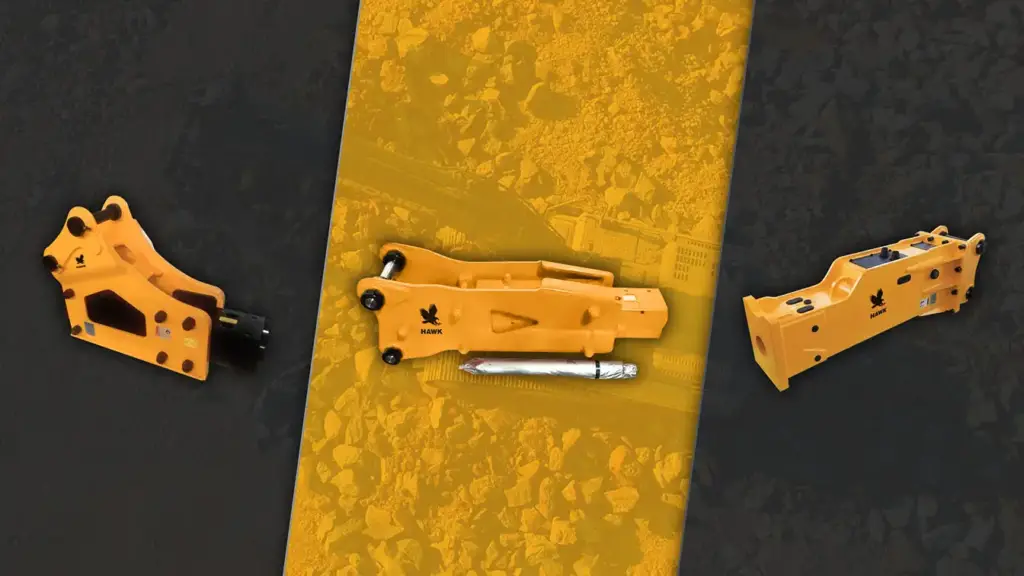
1. Introduction
Excavator jack hammers are indispensable tools in the construction and mining industries, providing unparalleled efficiency for breaking hard surfaces and materials. Understanding the types, features, and applications of these hydraulic hammers can significantly improve productivity, ensure safety, and optimize costs. This guide dives into everything professionals need to know about excavator jack hammers.
Excavator jack hammers, also known as hydraulic breakers, are powerful tools designed to crush, break, or chip materials like rock, concrete, and asphalt. Used in conjunction with excavators or carrier machines, these tools deliver high-impact energy, making them essential for tasks ranging from demolition to trenching. Their versatility and efficiency have made them a staple in industries like construction, mining, and roadwork.
2. Basic Components and Types
Understanding the components and types of excavator jack hammers is fundamental to selecting the right tool for excavation projects.
Key Components:
- Piston: Transfers energy to the breaker’s tool bit.
- Tool Bit: The part that directly impacts the surface, available in various shapes (chisel, blunt, or moil).
- Accumulator: Maintains hydraulic pressure for consistent operation.
- Housing: Encases the hammer, protecting internal components from damage.
Types of Jack Hammers:
- Hydraulic Breakers: Most common type, powered by the excavator’s hydraulic system.
- Pneumatic Breakers: Operated using compressed air, ideal for smaller jobs.
- Silenced Breakers: With soundless technology, suitable for noise-sensitive environments, offering operator comfort.
3. Primary, Secondary, and Specialized Applications
Excavator jack hammers are used in various applications across industries.
Primary Applications:
- Demolition: Breaking down concrete structures and walls.
- Roadwork: Removing old asphalt and concrete surfaces.
Secondary Applications:
- Trenching: Creating narrow excavations for utilities or pipelines.
- Rock Breaking: Splitting large rocks in quarries or mines.
Specialized Applications:
- Underwater Work: Hydraulic breakers designed for underwater operations.
- Recycling: Crushing concrete and other materials for reuse.
4. Essential Features to Consider
When choosing an excavator jack hammer, several features are essential for ensuring optimal performance and longevity:
- Impact Energy: Determines the hammer’s breaking power.
- Blow Frequency: Number of blows per minute, affecting productivity.
- Tool Bit Versatility: Availability of different bits for various applications.
- Noise Reduction: Features like soundproof housings for use in noise-sensitive areas.
- Anti-Vibration System: Reduces operator fatigue and enhances tool control.
5. Performance Factors
Performance is influenced by several factors, including:
- Hydraulic Pressure and Flow: Proper hydraulic power ensures efficient operation.
- Tool Bit Condition: Regular inspection and replacement of worn bits prevent performance degradation.
- Correct Alignment: Ensuring the tool is aligned properly with the surface maximizes impact and prevents damage.
- Maintenance Schedule: Regular servicing prevents breakdowns and extends tool life.
6. Carrier Machine Compatibility
Matching the jack hammer to the carrier machine is crucial for efficient operation.
- Excavator Size: The breaker’s weight and power should align with the carrier’s capacity to avoid imbalance.
- Hydraulic System Requirements: Ensure the excavator’s hydraulic output matches the hammer’s specifications.
- Attachment Mechanism: Verify that the jack hammer is compatible with the excavator’s coupler system.
Proper compatibility enhances performance and reduces wear on both the hammer and the carrier machine.
7. Selection Criteria and Cost Analysis
Choosing the right excavator jack hammer involves balancing performance with budgetary constraints.
Selection Criteria:
- Application Requirements: Define the material type, hardness, and work environment.
- Durability: Select models with reinforced housings and high-quality components for long-term use.
- Ease of Use: Opt for user-friendly models with simple control mechanisms.
Cost Analysis:
- Initial Investment: High-quality jack hammers may cost more upfront but provide better durability and efficiency.
- Maintenance Costs: Factor in expenses for tool bit replacements, hydraulic repairs, and periodic servicing.
- Operational Costs: Include fuel or energy consumption and operator wages when evaluating overall expenses.
8. Risk Assessment and Environmental Impact
Like all heavy machinery, excavator jack hammers come with inherent risks and environmental considerations.
Risk Assessment:
- Operator Safety: Ensure proper training and use of personal protective equipment (PPE).
- Equipment Damage: Avoid misuse to prevent structural damage to the hammer or carrier machine.
- Flying Debris: Use protective screens and maintain a safe work perimeter.
Environmental Impact:
- Noise Pollution: Use soundproofed hammers in residential or urban areas.
- Dust Control: Implement water spray systems to reduce dust during operation.
- Fuel Efficiency: Opt for energy-efficient models to minimize carbon footprint.
Adhering to safety guidelines and environmental best practices ensures compliance with regulations and promotes sustainable operations.
9. Conclusion
Excavator jack hammers are versatile, high-performance tools that play a vital role in modern construction and mining operations. From their basic components to their specialized applications, understanding their features, performance factors, and selection criteria can significantly enhance productivity and safety.
Choosing the right jack hammer involves considering factors like compatibility, cost-effectiveness, and environmental impact. By making informed decisions and adhering to best practices, professionals can maximize the efficiency and longevity of their equipment.
Investing in a right jack hammer and maintaining it properly not only ensures smooth operations but also reduces downtime and operational costs, making it an indispensable tool for any project requiring precision and power.